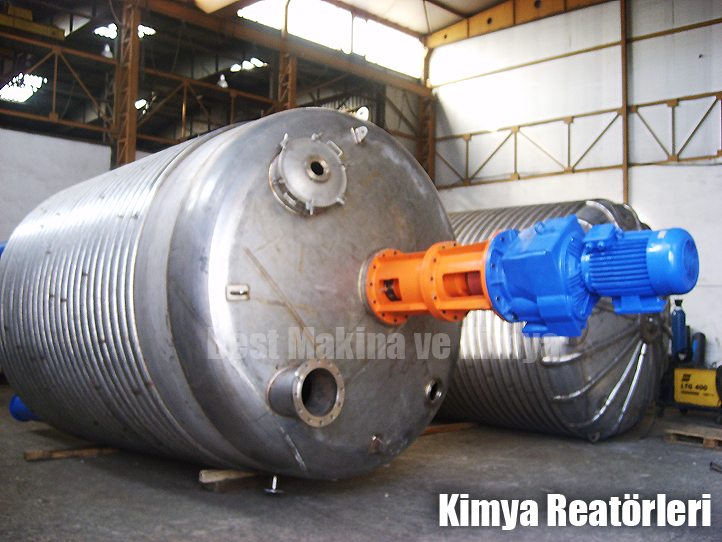
Reactors
Best Makina Kimya production within realized reactors, especially loaded into the different stages of the reaction in the chemical industry various liquid and / or solid raw materials (alkyd, polyester, PVA, etc.) is mixed with special agitators, if desired subjected to heating or cooling, pressure or under vacuum at temperatures specified mixtures are systems that provide a uniform way to react.
Reactor Units, 1-50 cubic meters according to their usage and location. in capacity it is produced according to customer’s request.
- Manufacturing is carried out and appropriate design to international standards.
- High quality and long life guarantee.
- AISI 304 , 316, 316L , 316Ti stainless steel is used and certified quality materials .
- The outer body of the jacket or half pipe coil , the coil inside the extruded pipe from the heating and cooling.
- 16 bar pressure and a 300 ° C temperature strength.
- Product specially designed agitators , there is a wave -breaking or crushing the foam .
- ATEX applications in hazardous Madiran performed .
- speed with inverter control options are offered .
- There is the possibility to access sensitive load cell weighing .
- Water Heaters can be manufactured cooled mechanical seals or soft seals .
Reactor
The reactor is a particular type of container commonly used in the chemical industry. Such solid dissolution vessels used in industry, product mixing, chemical reactions, batch distillation, crystallization, extraction and liquid or liquid is used in various chemical processes such as polymerization since they incorrectly identified. In some cases, there is a name that reflects the role they perform in unknown, as reactor.
A typical reactor, agitator, and a container formed from the extensive heating and cooling system. These containers vary in sizes from 20 liters to 40,000 liters. Usually steel, stainless steel, glass lined steel, glass, or are made of exotic alloys. Liquids and solids are charged via links in the reactor’s top cover. Vapors and gases are discharged by means links at the top of the reactor. Liquids are usually discharged from the bottom of the reactor.
Mixing
The mixer is made by mounting the center of the drive shaft by the drive unit located at the top. Propeller blades mounted on the shaft. A wide variety of blade designs are used, and typically includes blades 2/3 reactor diameter. In case of mixing the high viscosity adhesives that product side and reactor type anchor having a close clearance between the walls of mixers are used. Breaking Wave is designed to break the flow brought by a rotating mixer occur. These breakwaters are placed or fixed on the reactor, the reactor is mounted to the side walls.
Despite significant improvements in blade mixers and breakwaters design is limited by the large amount of energy applied to the reactor in the mixing process. The high rate held mixer loading will cause the shaft to create problems once stabilized. Where mixing is a critical parameter, the reactor is not an ideal solution. Much higher mixing ratios can be obtained using a small flow system with high-speed mixers. (Ultrasonic stirring or static mixers)
Heating – Cooling System
Heat transfer fluid in the coil even as products even in the reactor generally release heat during the reaction (exothermic ) or absorbed ( endothermic ) would . to keep the product temperature inside the reactor at the desired temperature , a cooling jacket or heated or cooled in a controlled manner out of the coil . Coils or extra jacket for heating and cooling the reactor . Jacket or heat transfer fluid circulates to increase or to decrease the temperature along the coil. the cleaning of the boiler external cooling jackets are preferred for the chemical and pharmaceutical industries is more easy. Heat transfer coefficient is also an important parameter.
External cooling jacket and is creating significant heat transfer restrictions due to the design of the coil must also accept large reactor .
Mixer Reactor
Best Makina Kimya implements polycondensation reactor in Europe’s most famous mixer by the company in the 90s Designed dihedral blade mixers in the year since the similar designs. Removal of double angle blade mixers in terms of shortening the reaction time and reaction water has great advantages.
Automatic Phase Separator
The amount aseotrop inside the reactor when using automatic phase separator in aseotropl reaction in the reactor so that the reaction is always the removal of water remains constant being the consistently high efficiency and energy savings are achieved.
Secondary Circulation System Heating / Cooling
Stainless Ertan who allows multiple units to independent operation of each unit in the facility which is heated and cooled with hot oil Saylam implement the secondary circulation system. Whereby the temperature of each unit separately heating the fat and / or the passage into the cooling phase is possible.
Technical Details
- 40,000 liter capacity 20 Litre-
- Pressure Vacuum – 6 Bars
- Heating-Cooling jacket, Half Pipe Coil and / or internal Serpentine
- A packed soft sealing (cooling by Operating Temperature Ring) or mechanical seals
- Material AISI 304 – 316 – 316Ti
- Drive IP54 or IP56 (Ex-proof) Motor Gear
- Made by Anchor Properties Type mixer to be mixed, Turbine, Two, Four or Double Angle Blade Type